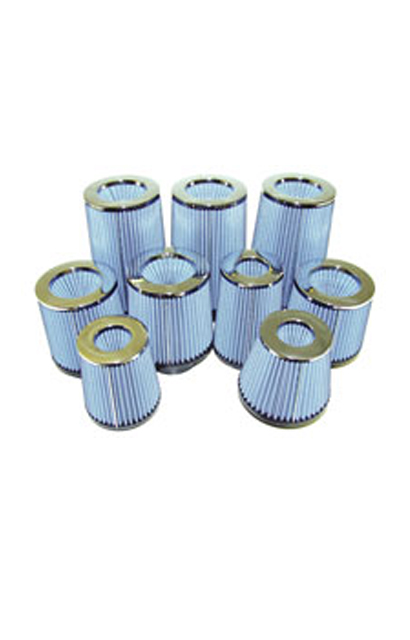
AMSOIL Ea®Universal Air Induction Filters
July 15, 2015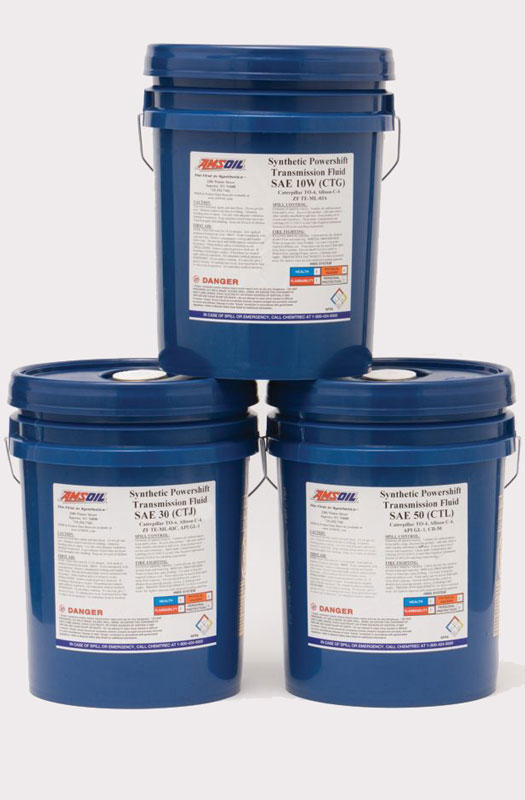
AMSOIL Synthetic Powershift Transmission Fluid SAE 10W
July 15, 2015DC Series Synthetic Ester Compressor Oil
AMSOIL DC Synthetic Compressor Oils are long-life, premium compressor lubricants based on novel, proprietary technology. They improve compressor efficiency and extend drain intervals in reciprocating (piston) compressors and vacuum pumps where high discharge temperatures or carbon build-up are a concern.
AMSOIL DC Synthetic Compressor Oils incorporate the highest quality, thermally-stable synthetic esters fortified with premium non-detergent, ashless additives for maximum protection at high temperatures and pressures where petroleum lubricants typically break down. (DCK & DCL)
AMSOIL DC Synthetic Compressor Oils are long-life, premium compressor lubricants based on novel, proprietary technology. They improve compressor efficiency and extend drain intervals in reciprocating (piston) compressors and vacuum pumps where high discharge temperatures or carbon build-up are a concern.
AMSOIL DC Synthetic Compressor Oils incorporate the highest quality, thermally-stable synthetic esters fortified with premium non-detergent, ashless additives for maximum protection at high temperatures and pressures where petroleum lubricants typically break down.
Improves Compressor Efficiency
AMSOIL DC Synthetic Compressor Oils are designed to prevent hard carbon deposits on valves for greatly improved compressor efficiency. Valve maintenance intervals are extended and recompression is virtually eliminated. AMSOIL Compressor Oils help reduce heat and improve compressor efficiency, saving money through lower electrical energy consumption.
Reduces Wear
Unlike other compressor oils, AMSOIL DC Synthetic Compressor Oils are anti-wear fortified. They help reduce wear in high contact regions for increased compressor life and efficiency.
Extends Oil Life
AMSOIL DC Series Compressor Oils combine the inherent oxidation resistance of synthetic esters with highly potent oxidation inhibitors. They last several times longer than petroleum oils, effectively reducing maintenance and waste oil disposal costs.
Reduced Oil Consumption
The low volatility, highly polar nature of AMSOIL DC Synthetic Compressor Oils reduces the amount of oil needed for cylinder lubrication compared to petroleum oils. Drip feed rates can be lowered, downstream oil is minimized and money is saved on make-up oil.
Resists Water Contamination
Water from condensation builds up in compressors that can cause oil/water emulsions, environmental discharge hazards and rust. AMSOIL DC Synthetic Compressor Oils readily separate from water, and they are anti-rust fortified. Water can be easily drained off for simplified environmental discharge and increased oil life.
Safety Advantage
AMSOIL DC Synthetic Compressor Oils are ashless, high flash point formulations with very low carbon-forming tendencies that minimize the incidence of ignition-promoting “hot spots.” While DC Synthetic Compressor Oils can provide improved fire safety, they cannot be considered non-flammable.
APPLICATION RECOMMENDATION
The appropriate viscosity of AMSOIL DC Synthetic Compressor Oil is recommended for use in rotary vane and reciprocating compressors and vacuum pumps. Drain intervals of 8,000 hours or more can be expected under normal operation. This is subject to operating conditions and maintenance practices. Monitoring by oil analysis is recommended.
Compatibility
DC Synthetic Compressor Oils are compatible with petroleum and most other synthetic-based lubricants (not compatible with polyalkylene glycol or silicone oils). For best performance, AMSOIL recommends the compressor be thoroughly drained and cleaned if needed prior to the installation of DC Synthetic Compressor Oils. If carbon deposits are present on the internal components, it is recommended they be removed following the manufacturer recommendations. For the first 500 hours of operation, check the filters regularly and clean or replace as necessary.
AMSOIL DC Synthetic Compressor Oils can be used with the following gases, paints, plastics and elastomers:
Gases: | • Nitrogen • Hydrogen • Helium • Carbon dioxide (dry) • Ethylene • Methane • Propane • Butane • Propylene • Butylenes • Natural gas • Benzene • Butadiene • Furnace (crack gas) • Hydrogen sulfide (dry) • Synthetic gas • Sulfur dioxide |
Paints: | • Epoxy • Oil resistant Alkyd. |
Plastics: | • Acetal (Delrin) (Celcon) • Phenolic • Polyamide-imide • Polyamide (nylon) • Polyetherimide (Nylon) • Polyimide • Tetrafluoroethylene (PTFE) • Terephthalate |
Elastomers: | • Fluoroelastomer (Viton) • Nitrile (> 36% Buena N) • Polyacrylate (HyTemp) • TFE Propylene (Aflas) • Florosilicone (Silastic) |
Note: Not recommended for “breathing air,” refrigeration compressors or for use with Chlorine, Oxygen, Hydrogen chloride, Ammonia or Sulfur hexafluoride gases. |
TYPICAL TECHNICAL PROPERTIES 10/10 | ||
Synthetic DC Series Compressor Oils | DCK ISO 100 | DCL ISO 150 |
ISO VG — ASTM D-2422 | 100 | 150 |
VK 100°C — ASTM D-445 | 11.3 | 13.7 |
VK 40°C — ASTM D-445 | 99.1 | 148.5 |
Viscosity Index — ASTM D-2270 | 100 | 86 |
Density — ASTM D-1298 | 7.747 | 7.851 |
Flash Point °C (°F) — ASTM D-92 | 250 (482) | 258 (496) |
Fire Point °C (°F) — ASTM D-92 | 282 (540) | 282 (540) |
Pour Point °C (°F) — ASTM D-97 | -40 (-40) | -31 (-24) |
Four-Ball Wear Test — ASTM D-4172: 40 kg, 1200 rpm, 75°C, 60 minutes, mm |
0.45 | 0.45 |
Copper Strip Corrosion Test — ASTM D-130 | 1A | 1A |
Foam, ml ASTM D-892. Seq I, II III at end of test | 0/0/0 | 0/0/0 |
Demulsibility ASTM D-1401 [oil/water/cuff (minutes)] | 40/40/0 (15) | 40/40/0 (15) |
Rust Procedure A ASTM D-665 | Pass | Pass |
Reviews
There are no reviews yet.